Get SWITCHED ON
with the RIGHT CHOICE!!!
It’s no surprise that most of us feel that each year passes more quickly than the last. As our lives move faster and faster in an everchanging technological world, it may seem surprising to know that Iffland Electrical has been established in our local area for over thirty two years servicing the electrical requirements of people within their homes and businesses throughout the community. Still family owned and operated, our company focuses on providing our clients with the best advice, service and value for money when it comes to electrical solutions for the home and work environments we spend countless hours living in. Our name and reputation are synonymous with the highest standards of excellence for our trade and we are multiple nominees’ and finalists in local business awards.
Iffland’s Electrical are proud of our long history and the fact we advertise our family name as our business gives our clients and the community the confidence and knowledge that engaging Ifflands is dealing with real local people with strong attachments to the local community. Our family name is the forefront of our business so you can be sure that choosing Iffland’s Electrical is your best decision and the right choice. Since our fledgling beginnings, our business has grown over the years to encompass a wider range of services other than just electrical for our clients. These include the supply, installation, repair and maintenance for a variety of services including Solar Panels, Commercial Washware and Cooking Equipment, Communications and Data Systems Security and CCTV Systems, MATV for free to air and pay tv systems. One of the many services we offer to our clients are any updates from within the industry that may impact the day to day operations within the homes and businesses each of us occupy each day. As such we would like to offer the following information for you to review regarding “safety switches” or RCDs and the current legislation as it exists for homes and businesses.
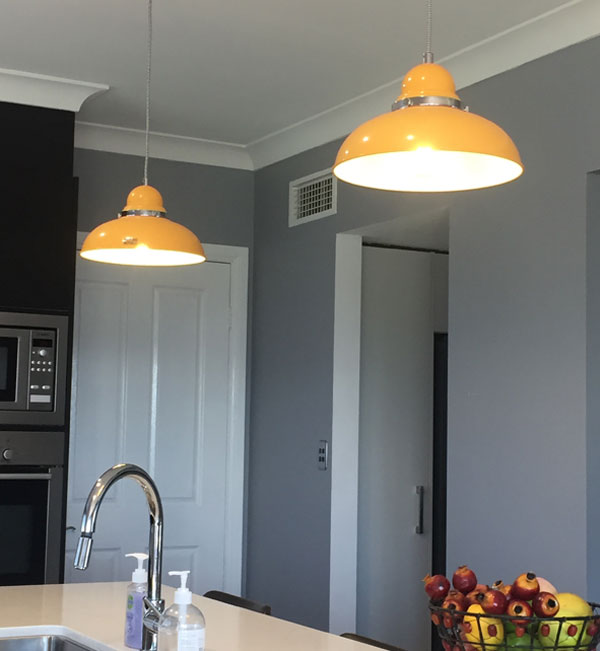
Work Health and Safety Regulation 2011– Electrical Equipment and Installations
On the 18th of February 2011 amendments were made to the Occupational Health and Safety Regulation of 2001 in Division 7 and published on the then NSW WorkCover website. These amendments listed the requirements for an employer to ensure the business provides a safe working environment for both the employer and staff. These requirements were specified in Clauses 62A and 62B of the OHS Amendment (RCD) Regulation 2011 and took effect on the 18th of February 2012. The legislation was revised under the Work Health and Safety Regulation (2011) in January 2013 and again in 2017 and updated as part of Chapter 4, Part 4.7, Divisions 3 and 6 – “Electrical Equipment and Installations” This revised legislation relates to electrical testing off electrical equipment and the installation of “safety switches” (or RCD’s) to protect all plug-in electrical items used by your staff and indeed the socket outlets themselves. That is, in layman’s terms, the general power points in your premises. The new legislation is very specific in its reference to both the employer and controller of the premises as to their responsibility in implementing and maintaining the new arrangements of the legislation.
Severe penalties can be imposed for those employers
and premise controllers (PCBUs) who may choose not to implement the new laws in their work environment.
We have provided a copy of the legislation below for your information. Either myself or my friendly staff would be happy to assist your business further with any clarifications concerning the introduction of any additional items or equipment necessary for your electrical installation to comply with the new legislation.
We will contact you to arrange a consultation with one of our representatives to discuss options and assist you.
I would like to thank you for your time in reviewing this letter and we look forward to helping you with a professional and cost effective solution for your business to implement the necessary changes to comply with the legislation.
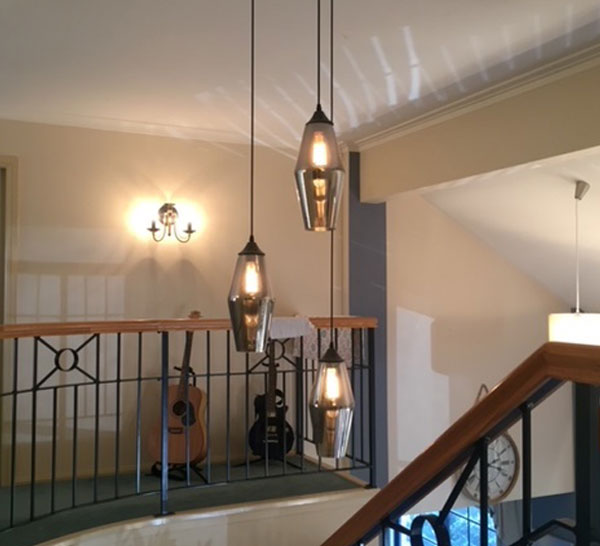